Swordsmithing has been a part of history and culture for millennia. Swords are symbols of power, craftsmanship, and honor. From the legendary katanas in Japan to the longswords that have dominated Europe for centuries, they’ve been a part of history. What goes into making these incredible weapons? Discover the world of swordsmithing, and how master craftsmen create these iconic weapons.
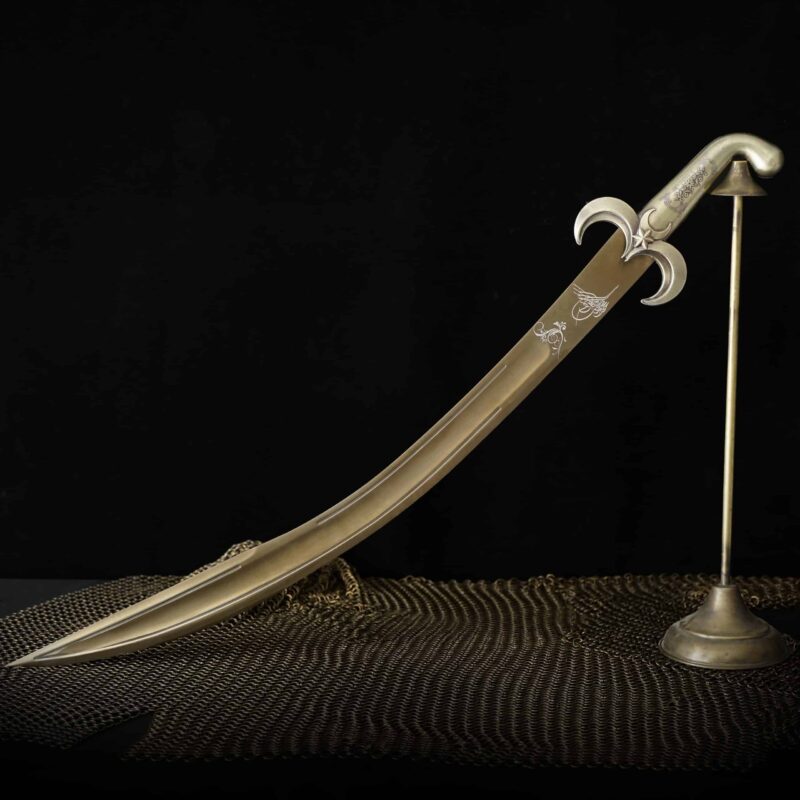
You may be interested in this article. Where is the Zulfiqar Sword?
History Of Swordsmithing
The history of swordsmithing dates back to the Bronze Age, when the first metal swords were created. Techniques evolved over the centuries as a result of different cultures and advances in metallurgy. While the Japanese mastered sword-making with their samurai swords, Europeans created robust and ornate swords that were used by knights and nobles. Each culture has contributed to the rich history of swordmaking with its unique designs and methods.
The Swordsmith’s Workshop
The traditional swordsmith’s workshop is an intriguing place filled with hammering sounds and glowing forges. Anvils, hammers and tongs are essential tools. Specialized equipment such as bellows and quenching tank are also housed in the workshop. Apprentices are vital to the future of the trade. They learn the craft from a master, and ensure that the skills and techniques will be passed on through the generations.
Materials used in Swordsmithing
Steel is the primary material used to make swords, but it‘s not any steel. For its hardness and ability hold a sharp sword, high-carbon steels are preferred. Swordsmiths also use a variety of materials, such as leather or wood for grips and precious metals to add decorative elements. Each material is selected for its unique properties that contribute to the overall quality and aesthetics of the sword.
The Process of Sword Making
Forging a Sword
Forging begins by heating the steel until it is red hot and then hammering into shape. The smith needs to be strong and precise in order to ensure that the metal is worked evenly. The sword is heated repeatedly and hammered to gradually take shape.
Annealing
After the basic shape has been achieved, the sword is annealed and tempered. The sword is heated and allowed to cool down slowly. This relieves internal stress. The sword is then quenched after being reheated at a lower temperature. This gives it the perfect balance between hardness and flexibility. This step is crucial for the sword’s durability and performance.
Sword Design and Geometry
Different sword shapes serve different purposes. Some swords have been designed to cut, while others are for thrusting. Others can be used for both. The geometry of the sword affects its balance, and therefore its effectiveness. These factors are important for swordsmiths to consider, as they want their work to be both beautiful and functional.
Sword Edge
Sharpening an edge is a skill in and of itself. The traditional method involves grinding the sword with whetstones in varying grits, then polishing it with finer stones. The edge is checked for sharpness and consistency to ensure it will perform well in combat or during ceremonial uses. To keep the edge sharp, regular maintenance is required. This includes periodic honing and care in handling.
Sword Fittings & Mountings
Fittings are essential to any sword. The hilt guard and pommel all work together to create balance and control. The hilt, guard and pommel are ornately decorated to reflect the intended use of the sword as well as the status of the owner. Sheaths and scabbards are used to protect the sword. They can also be beautiful works of art, made from leather, metal, wood or inlaid with intricate carvings.
Traditional vs. Modern Swordsmithing Techniques
Modern technology has also had an impact on swordsmithing. Laser cutting and CNC machining techniques can produce precise components. Many smiths prefer the traditional handcrafting method, as they value the connection between the craftsman, and the metal. Combining old and new methods allows for innovative designs, while still preserving ancient tradition.
Famous Swordsmiths & Their Masterpieces
The history of swordsmiths is full of legendary figures whose work became iconic. In Japan, masters such as Masamune produced swords with unmatched beauty and quality. Ulfberht, an Ulfberht in Europe, produced swords that were known for their craftsmanship and strength. Their legacy continues to inspire swordsmiths today, and their masterpieces continue to be highly valued by collectors and history buffs.
Swordsmithing and Popular Culture
Swords have a special place within popular culture. They are often seen in films, video games, and literary works. Swords capture our imagination, from the elegant swords of “The Lord of the Rings“, to the futuristic light-sabers of “Star Wars“. The cultural representation of swordsmithing has been renewed, and many enthusiasts are now interested in learning the craft or collecting replicas.
The Future of Swordsmithing
The art of swordsmithing is constantly evolving. Materials, like high-tech alloys or composites, have been redesigned to offer new possibilities. The role of museums and collectors in the preservation of historical techniques and masterpieces is significant. There are now educational programs and workshops that ensure the knowledge and skills of swordsmithing is passed down to future generations.
Conclusion
Swordsmithing combines history, craftsmanship, and culture. Master craftsmen’s dedication and skills result in iconic weapons that are both functional weapons and works of art. The enduring appeal of handcrafted swords will continue to inspire and captivate us as we look towards the future.
FAQs
The materials, craftsmanship, and design of a sword are what make it unique. Each swordsmith gives their swords a unique character, which makes it a one-of a-kind item.
For more information you can read this article
If you want to buy a good handmade sword, this is the products for you
The length of time it takes to make a sword depends on its complexity. The time required to make a basic sword is a few weeks. More intricate designs can take up to several months.
Please call us if you would like to have a special sword made. Our customer relations manager will give you accurate information
Anyone with patience and dedication can learn to swordsmith. There are many workshops and schools that offer beginner courses to help you learn the basics.
The Japanese katana is one of the most popular swords, especially those made by Masamune, the legendary swordsmith. Excalibur is another famous example, as it was the sword of King Arthur.
Ottoman swords are special swords that have a place in world history.
Keep your handcrafted sword clean and dry. This will prevent it from rusting. Oil the sword regularly and store it in an airy, dry location. After use, wipe the blade with a soft cloth and avoid excessive handling.
You can read this article for more information. How to Maintain a Handmade Sword?
Pingback: How to Maintain a Handmade Sword? - SwordBuy
Pingback: The Intricate Process of Modern Sword Design - SwordBuy